All systems are designed with exceptional flexibility, allowing them to be interconnected and configured or combined for a wide variety of tasks based on specific requirements. Potential adaptations include modifications to piping, new interconnections, or additional measurement and control technology. Customers also have the option to temporarily integrate their own equipment into the pilot plant to replicate the process as realistically as possible.
Content / available equipment:
1. Laboratory unit with thin-film evaporator
3. Thin-film dryer (vertical and horizontal)
5. VISCOFILM thin-film evaporator
6. Tube falling-film evaporator
8. Conclusion
Figure 1: The diagram illustrates the application areas of various evaporation technologies. By selecting or combining the appropriate technologies, GIG Karasek is capable of processing a very wide range of different substances and replicating these processes extensively in the technical center. @ GIG Karasek
1. Laboratory unit: feasibility studies and identification of process-relevant factors
The focus of the laboratory unit is on assessing feasibility. The goal is to determine whether the product can be successfully separated and if the process is technically viable.
Effective evaporation of the material plays a critical role in this, taking into account both atmospheric pressure conditions and potential vacuum requirements.
Furthermore, it is highly important to identify potential challenges in evaporation as well as other process-specific factors.
The laboratory unit consists of a tabletop system made of stainless steel, featuring a thin-film evaporator.
Figure 2: GIG Karasek laboratory unit with thin-film evaporator. @ GIG Karasek
Operating data of the laboratory unit in the technical center:
- Vacuum: > 0.005 mbar absolute
- Heating temperature: 20°C to 250°C
- Feed rate: 0.25 to 2 kg/h
2. Thin-film evaporator: separation and concentration of complex liquid mixtures
The thin-film evaporator is characterized by a gentle evaporation process and is used for both concentrating and purifying valuable substances.
This evaporator is suitable for various applications, including the concentration of structurally viscous media, the concentration of temperature-sensitive products, and the distillation of low-boiling valuable components. Additionally, it is employed as a reboiler in rectification systems and enables the purification of high-boiling products through distillation.
Pilot plant: adaptation of the optimum rotor type
The thin-film evaporator system in the technical center represents approximately one separation stage, utilizing thermal oil as the heating medium. The evaporator can be operated with various rotor and wiper blade configurations to replicate the full range of functions available in large-scale systems. This setup enables targeted testing to determine the optimal combination for specific customer requirements or products. Additionally, integration with a distillation column is possible.
The system's performance is determined through a mass balance.
Figure 3: Thin-film evaporator system in the technical center © GIG Karasek
Operating principle: short residence times and minimal thermal stress
The thin-film evaporator consists of a cylindrical, externally heated surface with a rotor inside. The rotor blades are designed to avoid contact with the heating surface, while special wiping elements ensure uniform distribution of the product and continuous transport of the product stream. At the same time, the wipers prevent fouling or clogging of the heating surface.
Short residence times of the product on the heating surface and minimal thermal stress enable a gentle evaporation process, ensuring high product quality:
- The mixture is first drawn from the feed tank and transported through a preheater to the top section of the thin-film evaporator.
- There, it is applied to the inner wall of the evaporator via a rotating distribution system, flowing downward as a thin liquid film toward the evaporator sump.
- During this process, the low-boiling components of the mixture (vapor) evaporate.
- To enhance evaporation efficiency, the liquid film is turbulently mixed and evenly distributed along the heating surface using a wiping system.
- The continuous renewal of the product stream in contact with the heating surface ensures a gentle evaporation process and, due to minimized thermal stress, maintains high product quality.
- The resulting sump product is discharged from the evaporator using a gear pump and collected as concentrate.
- Meanwhile, the vapor flows to the condenser, where it condenses on the tube side. The condensed vapor is either collected in weighing containers or pumped directly into a storage tank.
Optimized substance separation: integration with a distillation column
The thin-film evaporator can be connected to a distillation column in the technical center to maximize the efficiency of the separation process and enable the production of highly pure products:
- The process begins in the thin-film evaporator, where the mixture is evaporated as a thin film on the heated surface.
- The resulting vapor exits the thin-film evaporator on the right side and is directed into the downstream distillation column. In this configuration, the vapor that would normally flow directly to the condenser is rerouted to the column.
- Inside the column, which consists of two heated sections of tubing, the vapor rises. To improve separation performance, the tubes are equipped with special inserts (packings, bulk material) that are installed according to customer specifications.
- As the vapor ascends, it is diverted laterally at the top of the column as the overhead product, where temperature and pressure measurements are taken to monitor the process. The less volatile components of the mixture remain as the bottom product.
- To condense the vapor, it is directed downward through a discharge pipe into the condenser. There, it condenses and is ultimately collected as distillate in a storage vessel.
A typical application of this process is the desulfurization of biodiesel. In the first process step, the temperature-sensitive biodiesel is dehydrated in the thin-film evaporator. In the second process step, the column is engaged to separate the sulfur.
Operating data of the pilot plant in the technical center:
Thin-film evaporator:
- Throughput: 10 to 50 kg/h
- Process pressure: 5 mbar absolute to atmospheric pressure
- Maximum temperature: 340°C
Distillation column:
- Height: 1,587 mm
- Diameter: 107.1 mm
- Separation stages: Up to 15 stages possible
- Additional information: the throughput is the limiting factor for the column.
3. Thin-film dryer: gentle drying of heat-sensitive products
The thin-film dryer, a specialized design of the thin-film evaporator, provides a gentle and efficient alternative when conventional drying technologies reach their limits in demanding applications. The thin-film dryer is widely used in industries such as waste management, chemicals, pharmaceuticals, and food processing to effectively dry a variety of products, including sludges, chemicals, suspensions, pastes, and moist solids.
Figure 4: Operating principle of a thin-film dryer @ GIG Karasek
Pilot plant: maximum drying performance through dryer combination
The technical center is equipped with both a vertical and a horizontal thin-film dryer to conduct extensive tests and experiments.
For drying highly wet sludges, a combination of pre-drying in the vertical unit followed by post-drying in the horizontal thin-film dryer is recommended.
This approach enables the achievement of minimal residual moisture.
Figure 5: Horizontal dryer in the workshop © GIG Karasek
Operating principle: high efficiency with short drying times
The thin-film dryer operates on the principle of the thin-film evaporator and is distinguished by its high drying efficiency and capability for short drying times. With its specialized wiper design, the dryer enables gentle drying of liquid feed products, even to powder form, while minimizing valuable material losses and ensuring high purity of the dried products. A practical example of this can be found in our blog post: Precision Work at Power Oil Rostock, Germany.
Figure 6: Operating principle of the horizontal dryer @ GIG Karasek
Operating data of the pilot plant in the technical center:
Horizontal dryer / vertical dryer:
- Throughput: 10 to 40 kg/h
- Process pressure: 40 mbar absolute to atmospheric pressure
- Maximum temperature: 230°C
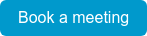
4. Short-path evaporator: high-performance distillation for sensitive products under low pressure
The short-path evaporator is an advanced distillation technology specifically designed for the gentle separation of sensitive substances under low pressure and high evaporation rates. The short-path technology is primarily used in the distillation of viscous and heavily contaminated products. The short-path evaporator can purify many substances that cannot be successfully separated using conventional thermal methods.
Pilot plant: integration with a thin-film system
The short-path evaporator in the technical center is an exceptionally efficient apparatus that enables gentle separation of sensitive media at low process pressures ranging from 0.001 to 1 mbar. Thanks to its flexible design, it can be tailored to meet the specific requirements of each product.
In the technical center, various types of wipers are tested and adjusted to determine the optimal combination for efficient separation.
An additional advantage of the pilot plant is its ability to be interconnected with thin-film evaporator systems. This configuration allows for the simulation of residence-time-critical evaporation processes, enabling realistic investigation and optimization of these processes.
Figure 7: Thin-film system in the technical center © GIG Karasek
Operating principle: maximum efficiency through an integrated condenser
Essentially, a short-path evaporator operates on the same high-performance principle as a thin-film evaporator, but with two key differences:
1. Fine vacuum: The product is distilled under fine vacuum (0.001 to 1 mbarA) to lower the boiling temperature, thereby avoiding unwanted reactions or decomposition of thermally sensitive products.
2. Integrated condenser: Unlike conventional evaporators, the condenser is directly integrated into the evaporator. This significantly shortens the path of the vaporized components (the vapor) to the condenser, minimizing pressure loss and enabling a high evaporation rate.
Due to its specialized design and fine vacuum process, the short-path evaporator is particularly suited for the gentle distillation of sensitive substances such as fatty acids, semi-volatile aroma compounds, vitamins, and oils.
Figure 8: Operational principle of the short-path evaporator @ GIG Karasek
Operating data of the short-path evaporator in the pilot plant of the technical center:
- Throughput: 10 to 100 kg/h
- Process pressure: 0.005 mbarA to 1 mbarA
- Max. temperature: 340°C
5. VISCOFILM – thin-film evaporator: gentle processing of high-viscosity fluids
The VISCOFILM thin-film evaporator has been specifically designed for the gentle evaporation of products with a high viscosity of up to 5,000 Pa·s. It serves as a bridge between conventional thin-film evaporators, which are designed for liquids with viscosities below 10 Pa·s, and polymer extrusion technologies that can handle liquids with viscosities of up to 10,000 Pa·s.
Operating principle: high-performance evaporator for sustainable applications
The VISCOFILM thin-film evaporator is based on the operating principle of a thin-film evaporator but features several distinctive characteristics. Its unique modular design and specialized rotor configuration set it apart, enabling versatile applications and a wide range of uses.
A key focus of the high-viscosity evaporator is the processing of renewable and/or recyclable materials, such as polymers. Its specialized design not only enables the efficient recovery of solvents but also minimizes residual content in the final products. The high-viscosity evaporator thus offers not only economic benefits but also contributes to reducing environmental impact and conserving valuable resources.
Figure 9: VISCOFILM thin-film evaporator system in the technical center © GIG Karasek
Pilot plant: robust equipment for continuous operation
The VISCOFILM thin-film system in the pilot plant is designed to be robust and is suitable for both continuous operation and small-scale production:
- Efficient processing of high-viscosity materials requires the use of a specialized feed pump to transport the material into the evaporator.
- Heating the entire system is essential to ensure that materials that solidify at specific temperatures can be effectively conveyed. For this reason, the entire VISCOFILM system is equipped with double-wall heating, covering everything from the feed tank and piping to the instrumentation, apparatus, and residue lines.
- Independent drives are provided for the evaporator and product pumps, ensuring precise control and regulation.
- The evaporator meets the strict requirements for use in Zone 1 hazardous areas.
- The self-cleaning effect enables continuous production.
Figure 10: Principle diagram of the VISCOFILM thin-film evaporator pilot plant © GIG Karasek
System equipment:
- Agitated tank with double jacket
- VISCOFILM thin-film evaporator
- Condenser
- Cooling trap
- Gear pumps: 10 - 150 l/h, motor with frequency converter
- Vacuum station (rotary vane pump / roots pump)
- Heating unit, cooling unit
- Evaporator, product pumps, and vacuum pumps
- ATEX category II 2G / 3G
- Temperature control units and control cabinet in non-Ex zone
Optimized integration of extruder and VISCOFILM evaporator
A distinctive feature of the VISCOFILM evaporator is the standard connection for an extruder. This setup allows the option of melting granulate directly in a temporarily provided extruder in the technical center and then feeding it into the VISCOFILM evaporator.
It is also possible to integrate the extruder downstream. A clear example of this is the customer-side installation of a cooler in the technical center to continue the process with an extruder after processing in the VISCOFILM evaporator. The cooler was specifically used to lower the product temperature from 240°C to 200°C before granulation. Additional equipment was provided by the customer to conduct realistic trials over a one-week period and optimally simulate the process.
Operating data of the VISCOFILM pilot plant in the technical center:
- Throughput: 10 to 150 kg/h
- Process pressure: 0.001 mbarA to atmospheric pressure
- Maximum temperature: 340°C
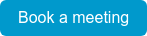
6. Tube falling-film evaporator: standard applications for low-fouling and low-viscosity media
Tube falling-film evaporators are widely used in standard processes where liquids need to be concentrated, mixtures separated, or valuable substances recovered. Their compact design makes them particularly well-suited for applications with low evaporation capacities. However, due to their demanding cleaning requirements, they are primarily used in industries that process low-viscosity and low-fouling media.
Pilot plant: multistage processes and trials with aggressive media
In the technical center, trials are typically conducted to assess the suitability of the tube falling-film evaporator for specific applications and to determine optimal operating parameters. Additionally, these trials support the development and validation of process models for scaling and implementing tube falling-film evaporators across various industries.
A key consideration is fouling, which can reduce heat transfer efficiency and evaporation performance. Furthermore, the combination of the falling-film evaporator with the thin-film evaporator allows for the simulation of multistage processes.
Operating principle: efficient evaporation through heat exchange and gravity
Tube falling-film evaporators are vertically arranged shell-and-tube heat exchangers that enable efficient evaporation with high vaporization rates through the combined effects of heat exchange and gravity:
- The product is introduced into the evaporator via the distribution tray in the upper apparatus head and flows as a thin film down the inner walls of the externally heated tubes.
- The more volatile fraction evaporates at the heating surface and is transported downward in a co-current flow with the concentrate under the influence of gravity.
- In the lower evaporator chamber, the vaporous phase (vapor) is separated from the liquid phase (concentrate).
- Any entrained droplets are removed from the vapor using integrated droplet separators or cyclone separators.
- The vapor is continuously discharged, while the concentrate at the bottom of the evaporator body is directed to the next evaporator stage or process step using a recirculation pump.
Figure 11: The tube falling-film evaporator is based on the principle of a shell-and-tube heat exchanger. @ GIG Karasek
Operating data for tube falling-film evaporator:
- Tube falling-film evaporator available in two sizes
- Product condenser with product cooler
- Evaporation capacity: approximately 500 to 2,000 kg per trial day
7. Distillation column
Distillation or rectification columns are widely used in various sectors of the chemical industry, particularly for the thermal separation of complex multi-component mixtures. They are especially advantageous when fractions need further separation to achieve higher purity levels. Common applications include the purification of recyclable substances, petroleum refining, and the large-scale production of basic chemicals.
Pilot plant: purification and separation of multi-component mixtures
In addition to the column that can be combined with the thin-film evaporator, the technical center also operates a standalone distillation column. Typical trial applications include the purification of mixtures and the separation of feed streams with components having similar boiling points, such as solvent recovery (e.g., ethanol) or the separation of fatty acids and resin acids from tall oil.
To optimize mass transfer, the column is equipped with packings or bulk material, increasing the surface area and maximizing contact between vapor and liquid. Customer-specified internal components can be provided for testing purposes and integrated into the column by GIG Karasek.
Note: if high separation efficiency is not required, such as in the straightforward separation of heavy and light boiling components (e.g., in biodiesel production), the short-path evaporator often proves to be a more cost-effective and less complex alternative. Learn more in our blog post “Biodiesel Distillation: Why the short-path evaporator is the better option compared to the rectification column.”
Operating principle: high purity levels through the countercurrent principle
The principle of the rectification column is based on the thermal separation of liquid mixtures through repeated evaporation and condensation. Ascending vapor and descending condensate interact continuously in a countercurrent flow, significantly enhancing separation efficiency and achieving high purity levels of the individual components.
- The liquid mixture is heated in the column’s bottom, causing the more volatile components to evaporate, rise through the column, and then condense in the downstream condenser. The heavier boiling fraction is continuously withdrawn from the bottom and disposed of.
- Most of the distillate is extracted as the overhead product, while a small portion is fed back as reflux into the top of the column to rinse the internals and ensure a consistently clean separation.
- As the vapor rising through the column condenses, it flows downward as a liquid counterphase. The mass and heat exchange between the ascending vapor and descending liquid phase facilitates the separation of the liquid mixture.
- Repeating the distillation process increases the concentration of the more volatile components in each subsequent distillate, eventually leading to the complete separation of the liquid mixture.
Operating data for the distillation column:
- Height: 3,342 mm
- Diameter: 108 mm
- Various packing and random packings available (customizable based on customer requirements)
8. Conclusion: explore, develop, optimize
GIG Karasek’s technical center provides state-of-the-art testing infrastructure and a team of experienced specialists to explore, develop, and optimize separation processes. With flexible equipment covering a wide range of temperature and pressure conditions, and the ability to integrate customer-specific apparatus, it serves as a comprehensive platform for laboratory and pilot trials. Customers can enhance separation efficiency, purity, and product quality while discovering tailored solutions for their unique requirements.
As a center of excellence for innovative separation technologies, the technical center supports the realization of customized solutions and is the ideal partner for developing optimal process solutions. Feel free to contact us to discuss your specific needs.
Visit our newsroom!
Here you can find the latest NEWS, our EVENT CALENDAR or further INSIGHTS featuring our key topics.
On the topic of our technical center we have published the following articles so far:
GIG Karasek Technical Center: how to test new concepts under real conditions
From Wastewater to Polymer Melts: Efficient Product Trials at the GIG Karasek Technical Center
MINIPLANTS - The Bridge Between Laboratory and Production