MINIPLANT for flexible location choice and hazardous media
Our MINIPLANT is a complete short-path distillation system delivered as a “plug-and-play” unit.
The compact unit…
- enables continuous small-scale processes, in contrast to many other methods that often rely on batch distillation in laboratory settings.
- is ideal for cost-effective production of sample products for potential customers.
Figure 1: Short-path Evaporator MINIPLANT © GIG Karasek
The system offers the following advantages:
- No water connection needed: Operating the MINIPLANT system requires only a power connection (400 V, 50 Hz, 25 kW). With air-cooled chillers, there’s no need for an external water supply, as cooling agents are self-contained within the system. This provides greater flexibility in site selection and reduces costs.
- Explosion protection: The system is designed for hazardous media (compliant with ATEX Directive 2014/34/EU; process chamber and environment: ATEX II 3/3 G Ex T3 Gc X).
- High viscosities: The system can handle viscosities up to 2,000 mPas.
- Fine vacuum: The system operates at a process pressure range of 0.01 to 1,000 mbar (absolute) and can achieve an ultra-fine vacuum for distillation, reaching pressures as low as 0.003 mbar (absolute).
- Data export: Process data is continuously recorded and can be accessed and exported at any time.
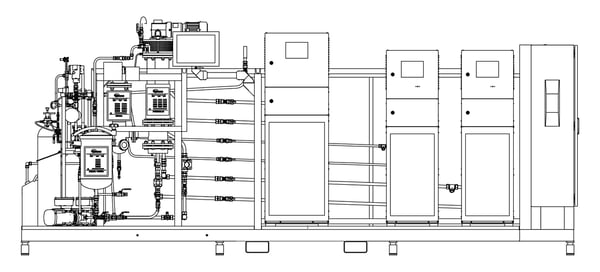
Figure 02: Short-path evaporation system, type SPE025-U © GIG Karasek
The MINIPLANT system includes the following main components:
- Feed tank
- Short-path evaporator heated with thermal oil, featuring an internal condenser
- Cold trap to protect the vacuum pump
- 3 gear pumps
- Vacuum pump
- Heating and cooling units
- Control cabinet with control system
- Operating panel
Table 1: Technical specifications of the main components of the short-path evaporator MINIPLANT system © GIG Karasek
Low thermal stress and short residence times
The short-path evaporator is a specialized type of thin-film evaporator in which the condenser is directly integrated into the apparatus to minimize the distance that vapor travels between evaporation and condensation. This configuration ensures gentle evaporation under fine vacuum conditions, ranging from 1 to 0.003 mbar (abs).
- The feed material is continuously transferred from the supply tank into the short-path evaporator, where it is distributed around the circumference by a rotating distribution system and moves down along the heated evaporator wall as a product stream. Movable wiper elements create a uniform distribution of the liquid film.
- Low-boiling components evaporate and subsequently condense on the internal condenser. The distillate is then discharged in liquid form.
- High-boiling components do not evaporate at the specific process pressure and are removed as a concentrated liquid stream from the short-path evaporator.
- Distillate and concentrate are transferred into collection tanks via gear pumps, with flow rates regulated by the speed of each pump. Alternatively, the collection tanks can be placed on platform scales provided by the customer.
- Non-condensed product vapors and inert gases are drawn through the vacuum connection, passing through the cold trap into the vacuum system. An efficient droplet separator on the rotor prevents heavy-boiling components from being carried into the vacuum system.
Figure 3: Schematic diagram of the short-path evaporator MINIPLANT system © GIG Karasek
Maximum efficiency and flexibility: the advantages of the MINIPLANT system
The specialized design of the short-path evaporator MINIPLANT offers a range of advantages:
- Wide application range: The system has a broad field of applications, especially in the production/recovery of valuable materials. Its functionality also covers nearly all applications of a thin-film evaporator.
- High cost efficiency: Thanks to its standardized design, a compact, all-in-one system can be implemented at affordable costs.
- Gentle evaporation: The MINIPLANT is optimized for the efficient evaporation of thermally sensitive products, which cannot be effectively separated by conventional thermal processes. It is ideally suited, for instance, for processing extremely temperature-sensitive products like lactic acid or fatty acids, as well as for the distillation of high-boiling-point components such as biodiesel or used oil.
- Low pressure drop: The integrated condenser in short-path evaporators results in extremely low pressure loss within the system. The evaporator’s optimized geometry significantly reduces the pressure drop between the evaporator and the condenser, enabling a high evaporation rate under high vacuum conditions.
- High flexibility: The short-path evaporator allows for a wide range of parameters in single-stage processes. Various flow rates, adjustments in heating, and rotor speed can be modified to achieve optimal operating conditions.
- Prevention of fouling: Due to the evaporator’s rotating design, fouling is prevented during operation. The wiper blades sweep just above the heating wall, ensuring continuous mechanical cleaning of the heating surface and reliable operational performance.
Figure 4: Short-path evaporator MINIPLANT © GIG Karasek
System performance in detail: energy requirements and product characteristics
The performance of the MINIPLANT system primarily depends on the product, pressure, and temperature conditions. The pumps are designed with a delivery capacity ranging from 3 to 25 liters per hour. However, the actual performance of the evaporator varies significantly based on specific product properties such as enthalpy of evaporation or viscosity.
1. Nominal performance of the MINIPLANT system
The hydraulic capacity of the short-path evaporator is exemplified in the following nominal performance table (kg/h) for methyl tert-butyl ether (MTBE), ethanol (EtOH), and water.
Table 2: Nominal performance in kg/h © GIG Karasek
2. Evaporator Performance as a Function of Heating Temperature
For products with a high enthalpy of evaporation, such as water, a large amount of energy is required for evaporation. In this case, the available energy becomes the limiting factor for the evaporator's performance. In contrast, products with a lower enthalpy of evaporation, such as methyl ether or ethanol, require less energy for evaporation and achieve significantly higher evaporation performance.
Figure 5: Theoretical evaporator performance as a function of heating temperature. © GIG Karasek
Figure 6: Short-path evaporation MINIPLANT © GIG Karasek
Conclusion: MINIPLANTS – when lab experiments scale up
GIG Karasek’s MINIPLANTS provide the perfect solution for companies seeking a cost-effective yet powerful stand-alone option. With the short-path evaporator MINIPLANT system, companies can cost-effectively optimize and scale up their production processes. The system is suitable for use with explosive media, offering greater flexibility in location choice and the ability to perform continuous processes on a small scale.
MINIPLANTS thus bridge the gap between laboratory and production facilities, making a valuable contribution to the innovation and competitiveness of companies.