Tube Falling-film Evaporator
Home
- / GIG Karasek Portfolio Overview
- / Tube Falling-film Evaporator
From the smallest evaporation capacities, for low-viscosity and moderately fouling media
Our tube falling-film evaporators are used in many standard applications and especially for smaller evaporation capacities.
We apply our extensive technical know-how in particular to droplet separation and cleaning of the apparatus and offer customized solutions.
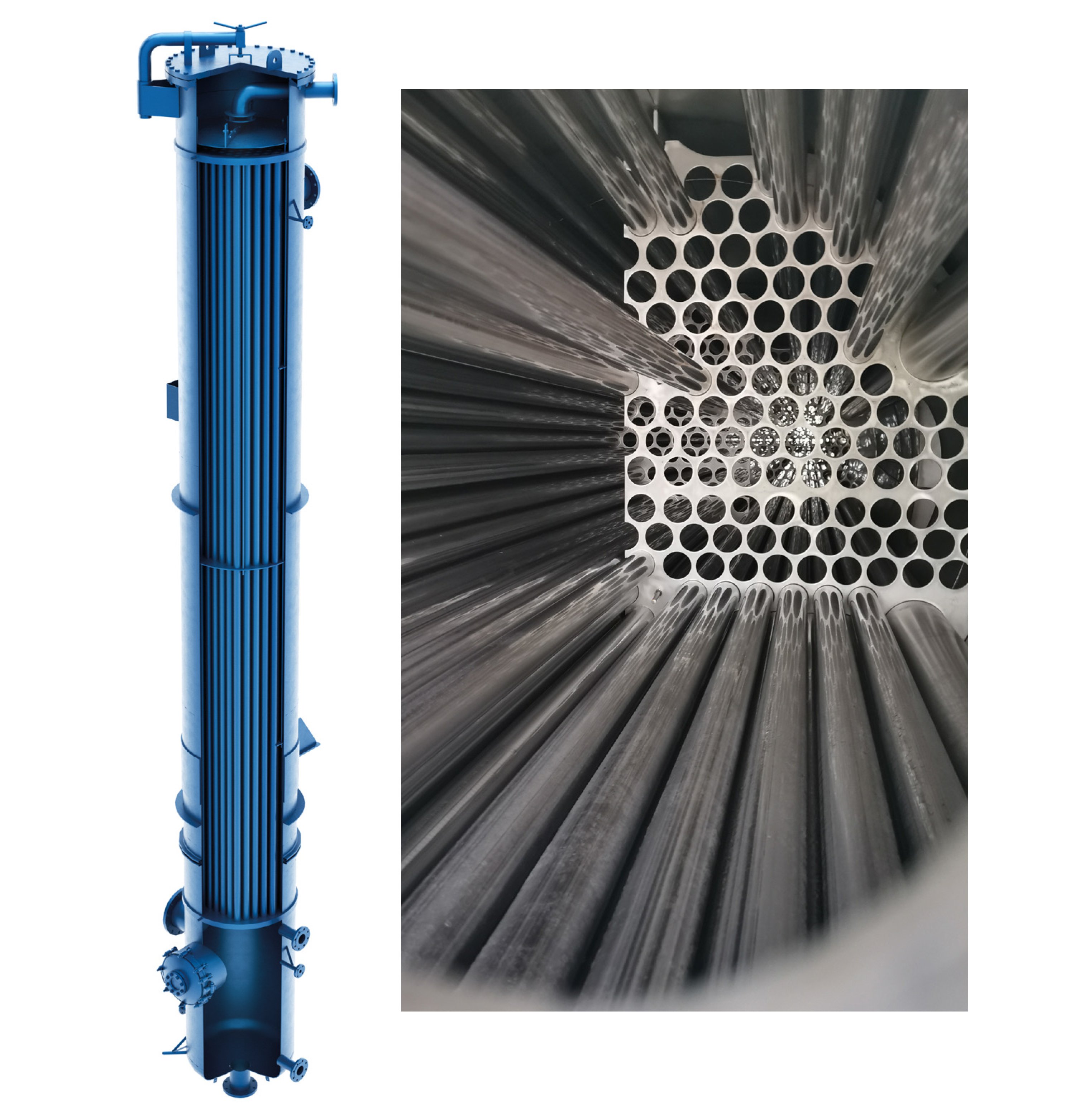
© GIG Karasek
In-house production
Like our plate falling-film evaporators, our tube falling-film evaporators are also manufactured in-house and tested to the highest quality standards.
ADVANTAGES
-
Ideal for low evaporation rates
-
Can be used flexibly for a wide range of industries and moderately fouling media
-
Optimized droplet separator design
-
Cost-effective cleaning
-
Compact design and small footprint
Functional principle
The medium to be thickened is thickened via vertically aligned tube bundles. The substance forms a thin film on the inside of the tube and flows downwards with gravity.
Vaporization of the more volatile medium on the heating surface produces steam, which is channeled in the tubes in co-current with the boiling liquid.
The vapor phase is then separated from the liquid phase in the lower evaporator chamber via integrated droplet separators or cyclone separators. Steam is generally used to heat the evaporator on the shell side.
Areas of application
-
Concentration of moderately fouling liquids and wastewater
-
Volume reduction of liquid-liquid mixtures
-
Recovery and separation of solvents like alcohols
-
Separation of multi-component mixtures and separation of water
-
Recovery of valuable materials
Typical operating parameters
-
Dimensions: 50 – 10.000 sqm
-
Feed rates: 500 kg/h – 150.000 kg/h
-
Operating pressure: ≥ 80 mbar abs.
-
Heating temperature: ≤ 200°C
-
Operating pressure: -1 / +20 bar(g)
-
Viscosity: ≤ 250 mPas
Optimization
For optimization, multiple evaporator stages can be integrated into a single unit, significantly increasing the evaporation performance.
Cleaning in case of fouling
To ensure efficient operation and consistent evaporation performance, regular washing cycles should be carried out depending on the medium. During planned downtimes, additional manual cleaning can be performed. The use of cleaning chemicals is also a feasible and effective option if needed.
For media that are particularly prone to heavy fouling, there is a risk of complete blockage of the tubes. In such cases, cleaning is often no longer possible, and the affected tubes must eventually be sealed off.
As an alternative, GIG Karasek offers the plate falling-film evaporator.
Other tube-type evaporator designs
GIG Karasek also provides other evaporator designs in tube design, including:
-
Rising film evaporator
-
Forced circulation evaporator
-
Natural circulation evaporator
However, due to significantly higher operating costs and lower evaporation rates, these technologies are now rarely used.
In addition, we supply condensers, heat exchangers, preheaters, and other components in tube construction.
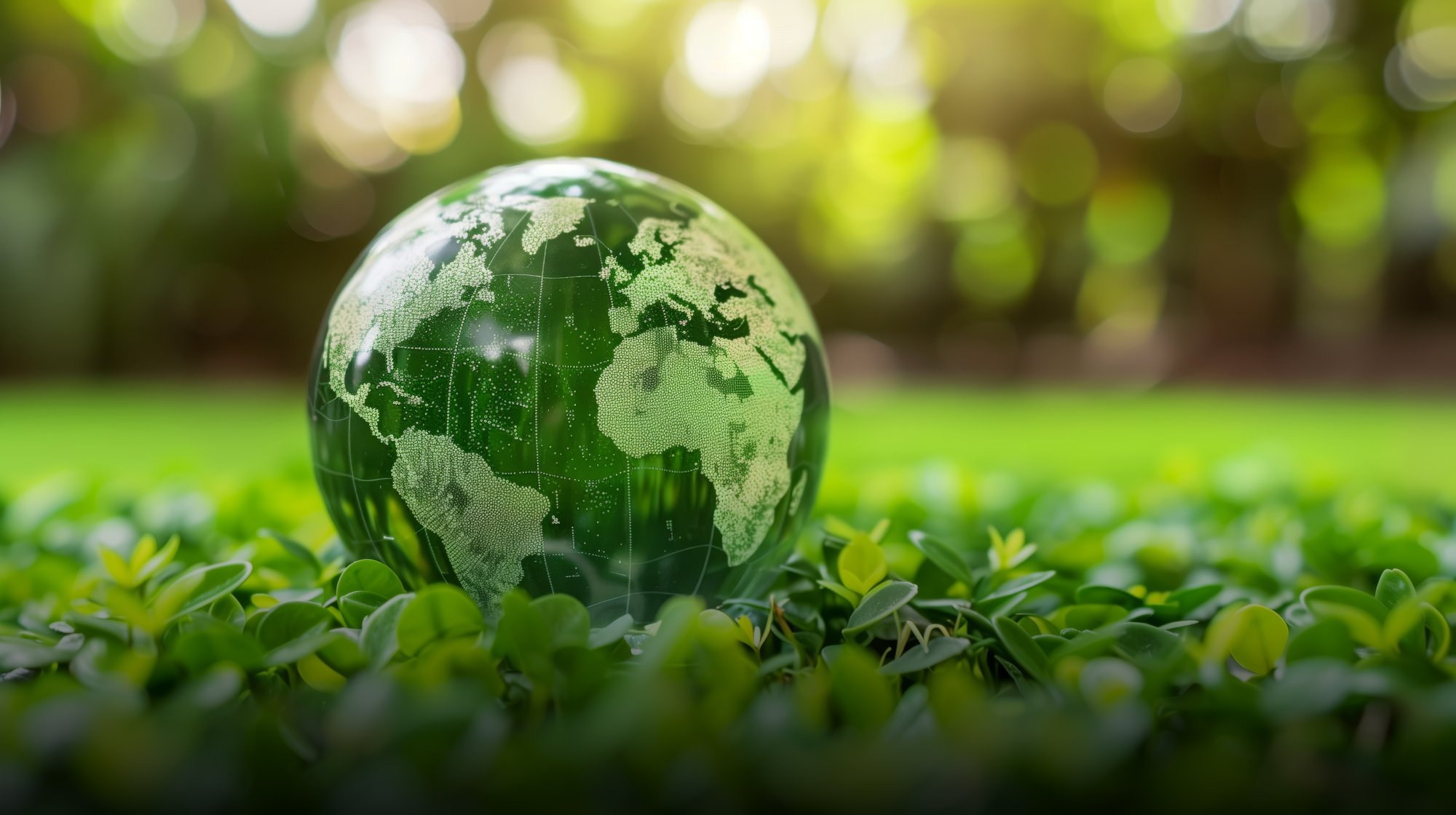
Visit our Newsroom!
Here you can find the latest NEWS, our EVENT CALENDAR or further INSIGHTS featuring our key topics.