Plate Falling-film Evaporator
Home
- / GIG Karasek Portfolio Overview
- / Plate Falling Film Evaporator
For high evaporation rates, low-viscosity, and highly fouling media
Our plate falling-film evaporators stand out for their exceptional quality, outstanding energy efficiency, superior condensate quality, and remarkably long service life.
We ensure these qualities through our many years of experience in design, the consistent automation of processes, and our extensive expertise in welding technology.
© GIG Karasek
In-house production
All components are manufactured in our state-of-the-art, in-house production facility in Gloggnitz, Austria, and are subjected to the strictest quality controls.
To meet individual customer requirements, GIG Karasek produces and delivers high-quality lamellas in various formats and materials. Thanks to our specially developed plate-forming process, we are able to offer optimized spot- and laser-welded lamellas.
GIG Karasek Lamella Technology
ADVANTAGES
-
Ideal for heavily fouling media
-
Highest evaporation rates
-
Excellent separation of liquid and vapor phase
-
Optimized spot-welded and laser-welded lamellas
-
Long service life
-
Minimal risk of fouling and corrosion
-
Energy-optimized design
-
-
Integrated droplet separator
-
Condensate separation thanks to secondary heating surface
Functional principle
The medium to be thickened is concentrated along the plate-type heating elements (lamellas), which are arranged as a bundle in the evaporator. The more volatile component is evaporated and removed from the apparatus. Optimized distribution systems are used to ensure the best possible distribution of the medium on the heating bundle and thus a high evaporation rate.
Areas of application
-
Concentration of black liquor, spent sulfite liquor, and waste water
-
Recovery and separation of solvents and alcohols
-
Volume reduction of liquid-liquid mixtures
-
Separation of multi-component mixtures
-
Water separation
-
Concentration of the liquid phase of fermentation residues in biogas plants
Typical operating parameters
-
Dimensions: 300 – 10.000 sqm
-
Feed rates: 5.000 kg/h – 150.000 kg/h
-
Operating pressure: ≥ 80 mbar abs.
-
Heating temperature: ≤ 200°C
-
Operating pressure: -1 / +5 bar(g)
-
Viscosity: ≤ 250 mPas
These are typical, exemplary operating conditions. Additional parameters are available upon request.
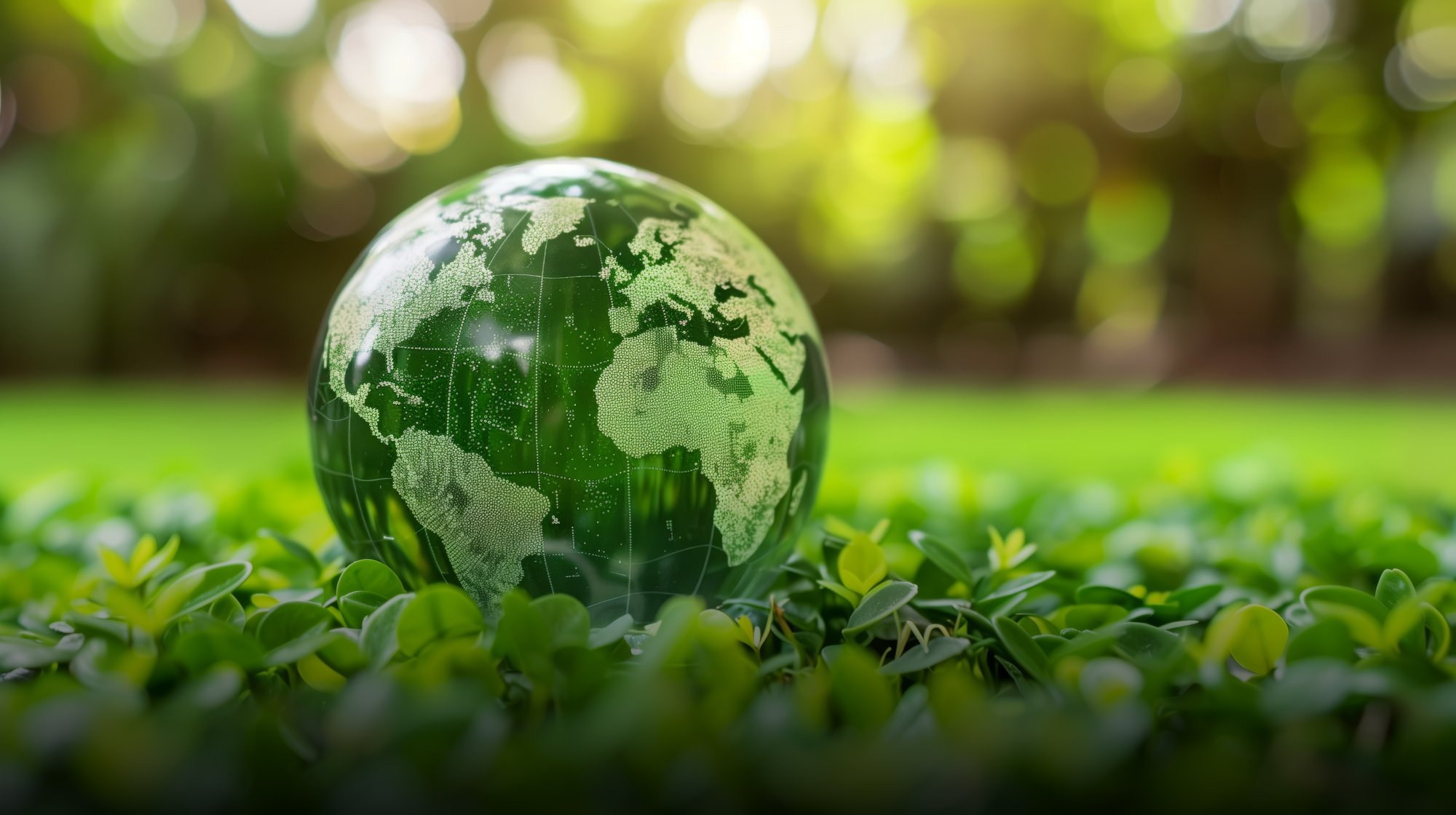
Visit our Newsroom!
Here you can find the latest NEWS, our EVENT CALENDAR or further INSIGHTS featuring our key topics.
Read our articles specifically on the topic of sulfite spent liquor or download our Whitepaper Sulfit Liquor!