Lamella Technology
Home
- / GIG Karasek Portfolio Overview
- / Lamella Technology
POWER Spot and LASER Luxe Lamellas
GIG Karasek manufactures lamellas in a wide range of formats and materials, using various welding techniques.
For decades, producing lamellas for plate falling-film evaporators has been one of our core competencies. We continuously refine this expertise with a strong focus on maximum quality and efficiency. The heating elements are produced in-house at our plate manufacturing facility in Gloggnitz, Austria – under strict quality standards.
Plate manufacturing facility in Gloggnitz, Austria © GIG Karasek
Highest quality begins in the detail
Find out more in our comparison - GIG Karasek Lamellas versus standard laser-welded lamellas on the market
ADVANTAGES
Highest evaporation rates, optimum cleaning possibilities and minimal corrosion, even for heavily fouling substances
-
Flexibility in terms of formats, materials, welding processes and customer-pecific requirements
-
Minimal risk of fouling
-
Minimal risk of corrosion
-
Long lifetime
-
Optimum utilization of heating surface
-
Optimized spot- and laser-welded lamellas
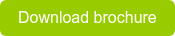
POWER Spot Lamella
Spot-welded heating elements
Our spot-welded lamellas are characterized above all by their resistance to fouling and corrosion, as the welding spot does not come into contact with the substance.
In a forming process specially developed by GIG Karasek, the welding spots are not exposed to any force during the forming process of the lamellas. This minimizes material deformation and stresses at the welding spot. In combination with our fully closed edge welding, the product impresses with a very long lamella lifetime.
The distances between the welding spots are adapted to the respective application. This means that spot-welded lamellas can be designed with a larger plate volume, reducing pressure losses during operation.
LASER Luxe Lamella
Laser-welded heating elements
With our laser-welded lamellas, we apply the advantages of our special forming process and thus minimize the stresses at the weld seams. The edges of the lamellas are designed identically to the spot-welded lamellas.
However, thanks to our forming process, we can also implement the larger plate volumes for minimal pressure losses for laser-welded lamellas. Thus, we offer an advanced version of the standard laser lamellas for maximum lifetime.
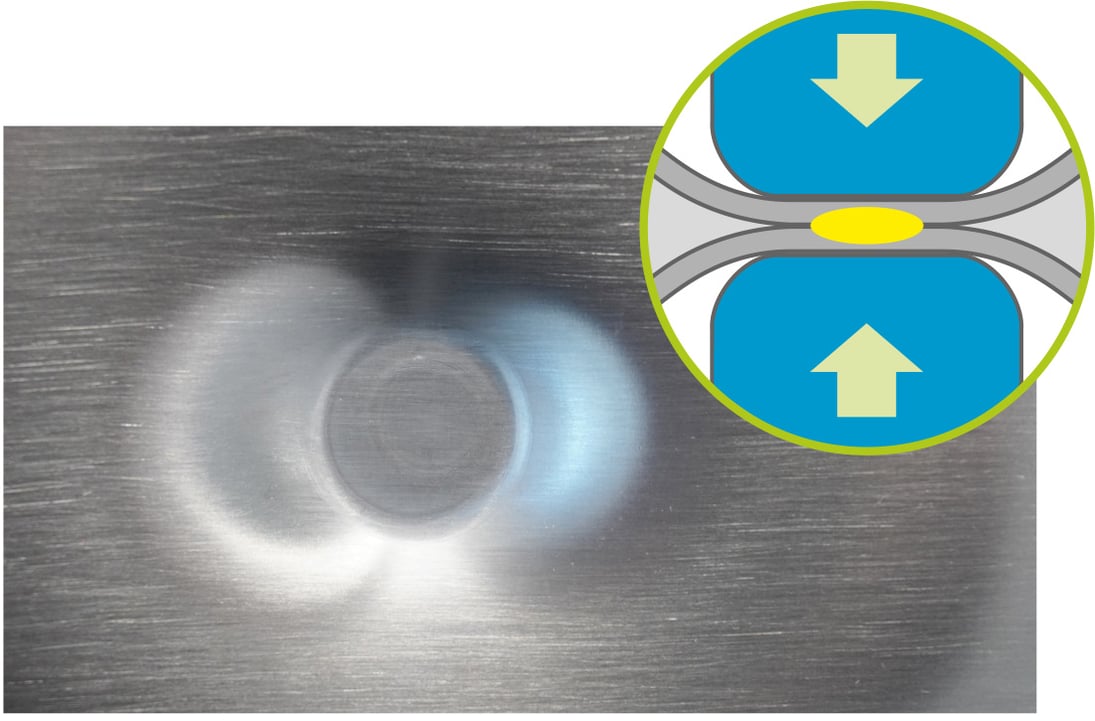
POWER Spot Lamella - Spot welding features a very smooth surface.
© GIG Karasek
LASER Luxe Lamella - Ring-shaped weld seam with laser welding
© GIG Karasek

Revamping, retrofitting and debottlenecking
Small but targeted changes often make a big difference when it comes to ...
-
maintaining systems and equipment at the highest level of performance over the entire ifetime or prolonging the lifetime ...
-
adapting production processes to changed circumstances or ...
-
increasing production efficiency.