Revamping, Retrofitting & Debottlenecking
Home
- / GIG Karasek Portfolio Overview
- / Revamping, Retrofitting & Debottlenecking
Practical alternatives to increase efficiency
GIG Karasek assists customers with the modernisation of their existing components and complete plants, regardless of the project scope.
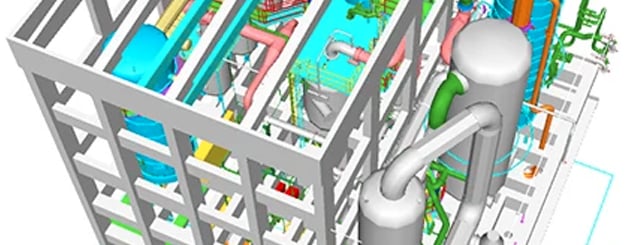
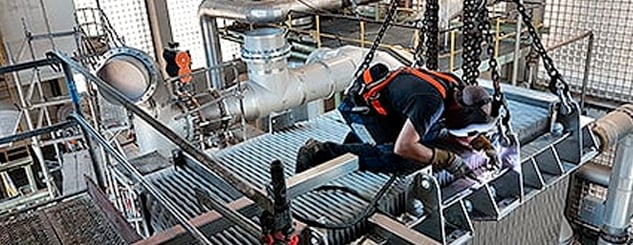
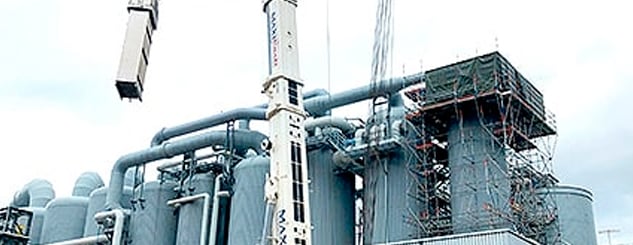
The life cycle of equipment and plants is characterised by numerous modernisations, optimisations and adjustments. Ensuring compliance with new regulations, circumstances and framework conditions can often be a costly challenge. New investments and acquisitions often appear at first glance to be the “simplest” and “most effective” solution. However, they are often not even necessary.
GIG Karasek offers three distinct approaches:
REVAMPING = maintenance / improvement of the device/system’s condition
RETROFITTING = upgrade / conversion
DEBOTTLENECKING = elimination of bottlenecks
By drawing on our extensive experience and specialist manufacturing knowledge, we can provide efficient and sophisticated solutions for the reconditioning of dirty, damaged or obsolete components and systems.
Modernising a machine or plant lets you avoid cost-intensive new investments.
Therefore, it is advisable to perform a comprehensive analysis and review of the initial situation – to be certain of getting the best out of your existing equipment! GIG Karasek can also support you during the initial search for solutions and subsequent decision-making process. Inventories, simulation models, the generation of multiple variants and various studies all provide a sound basis for this.
Overview
Recycling of a different kind
These days, recycling and environmental protection are always key concerns. The associated tasks can be accomplished in many different ways. Resource-saving and environmentally friendly processes can be provided by means of minor upgrades, adjustments or adaptations – often without significant expense.
Efficient production processes require sophisticated custom solutions,especially if the machines and plants concerned have been in use for several decades.
Our experts are available to support you here with inventories and appraisals. Based on the initial situation, our specialists analyse and validate unique approaches and solutions to achieve the best possible results.
We then work with our customers to develop a tailor-made modernisation strategy for the implementation of the concept.
GIG Karasek has decades of experience and comprehensive know-how in the fields of revamping, retrofitting and debottlenecking – and can therefore offer cost-saving and efficient alternatives to expensive new investments. This ensures that the project expenditure remains manageable in all areas.
However, modernisation is not always expedient, effective or feasible – GIG Karasek will discuss your options with you.
There are many reasons to opt for modernisation:
- As an alternative to new investments
- To increase capacity / capacity utilisation
- To improve energy efficiency
- To extend the life cycle
- To minimise downtime
- To ensure compliance with current rules and regulations
- To optimise product quality
- To improve infrastructure
Services provided:
- Assessments and inventories on site
- Detailed checks and inspections
- Development of a modernisation strategy or an expedient modernisation concept
- Supervision of dismantling/disassembly work
- Supply of replacement equipment, exchange of obsolete components
- Supervision of installation and commissioning work
- Warranty services for new components supplied by GIG Karasek
Revamping
Effective maintenance through reconditioning
REVAMPING is an effective way to modernise “outdated” equipment and plants. Targeted reconditioning of individual components makes the machine or system almost as good as new. The positive results include guaranteed compliance with current quality criteria and specifications as well as the certainty that all technology is now state of the art.
Professional preparation is crucial for REVAMPING. To start with, the components’ current condition is checked before they are prepared or revised accordingly.
The downtimes are kept as short as possible to minimise any loss of production and the associated costs.
In addition to the usual advantages of modernisation, REVAMPING also has additional positive side effects. These include increased operational safety and environmental sustainability, as well as optimised efficiency without a significant change in operations.
GIG Karasek’s REVAMPING service ensures that after the overhaul, the equipment and
systems perform at least as well as at the start of their life cycle, depending on the initial technical status or condition of the equipment concerned.
GIG Karasek – equipment
We understand your application and keep detailed records of all components manufactured by us. On the basis of each component’s specifications, this enables us to optimally adapt the modernisation process to your needs to achieve maximum performance and/or update the technology as required. Furthermore, this expertise ensures that you benefit from maximum quality and safety.
Special – equipment (from other manufacturers)
In addition, reconditioning and conversion of components (or even complete units) from other manufacturers are possible. Just as with our own machines, GIG Karasek delivers modernisation at the highest level.
Here too, our decades of know-how, profound expert knowledge and continuousfurther development ensure optimum results for our customers.
Retrofitting
Targeted updates – efficient, coordinated and cost-saving
RETROFITTING means replacing and/or expanding selected components to ensure compliance with current specifications and standards.
By means of specific, tailored retrofitting or conversion measures, the existing plant can be repaired so that operations can continue as before.
Successful RETROFITTING depends on an on-site assessment and inventory by our experts. These findings are used to draw up a suitable, efficient and cost-saving action plan in order to optimize the update sequence and keep downtimes during the RETROFITTING as short as possible.
The benefits
- An alternative to new investments
- Extended life cycle
- Adaptation to new framework conditions
- Unchanged plant operation
- Guaranteed spare parts availability
- More efficient production
- Quality enhancement
- Minimised downtime
- Improved energy efficiency
Debottlenecking
Increase efficiency by eliminating bottlenecks
DEBOTTLENECKING means investigating any bottlenecks in the process and then systematically removing them to unlock additional production capacity. In this way, efficiency – and thus profits – can be increased at minimal cost.
Understanding the bottlenecks in a system is the decisive step in the DEBOTTLENECKING process. Therefore, a comprehensive investigation and analysis of the overall operating conditions is essential.
However, plant safety must never be compromised as a result of the DEBOTTLENECKING measures.
Bundle replacement – simple yet effective
Bundle replacement is a classic example of expedient and efficient DEBOTTLENECKING – especially in older falling film evaporators.
The principle is quite simple – in existing falling film devices, not only are the discarded bundles replaced, the evaporation surface and thus the capacity are simultaneously increased thanks to larger plate dimensions. And with minimal effort and cost!
GIG Karasek manufactures plate bundles for this purpose in our in-house production facility, entirely in accordance with your individual requirements. Years of research and development in the field of welding and production technology guarantee the highest quality standards.
The plates are manufactured using resistance spot welding processes and therefore offer maximum reliability, quality and safety. Long product life cycles are ensured thanks to a minimised risk of contamination and corrosion.
Due to many years of experience as well as ongoing development and training, the experts at GIG Karasek are unique specialists worldwide in the field of DEBOTTLENECKING.
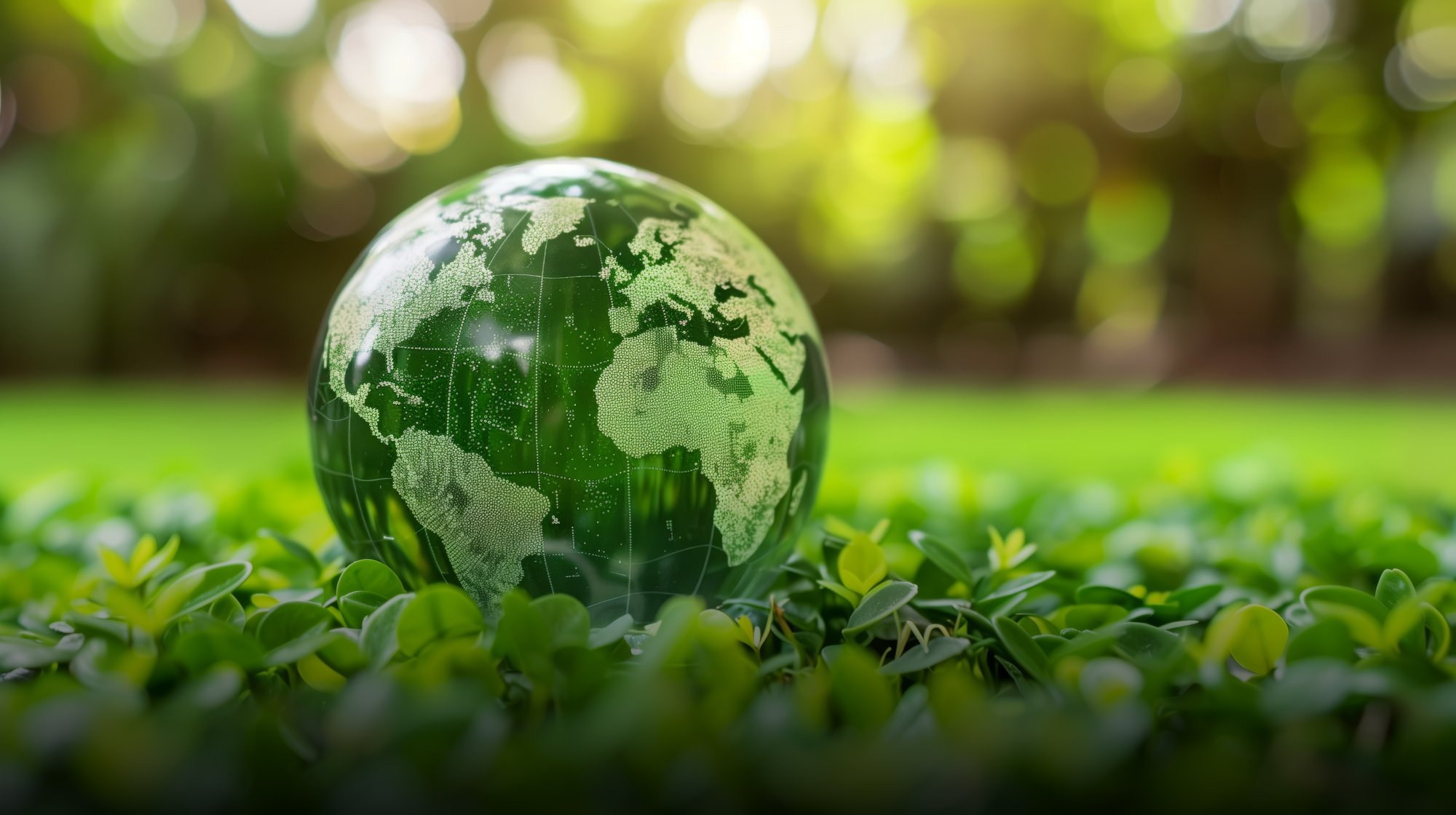
Visit our Newsroom!
Here you can find the latest NEWS, our EVENT CALENDAR or further INSIGHTS featuring our key topics.
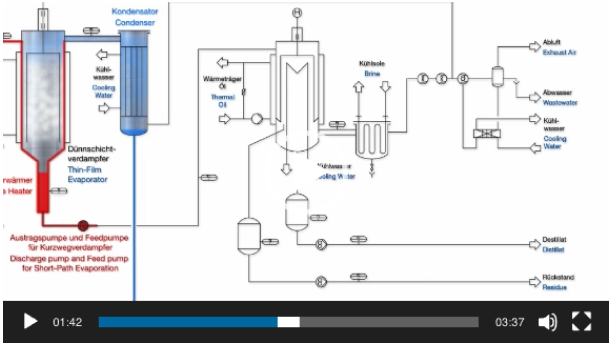
The product is distributed continuously over the entire circumference of the heating wall. Using special wiper elements the wall contact is renewed constantly and the product stream simultaneously transported. The blades do not touch the heating jacket, but prevented crusting or clogging of the heating surface by massively built, arranged with defined gap wiper elements.