Alle Anlagen sind äußerst flexibel konzipiert und können miteinander verbunden sowie je nach Anforderungen für verschiedenste Aufgaben konfiguriert und kombiniert werden. Mögliche Adaptierungen beinhalten die Anpassung von Rohrleitungen, neue Verschaltungen oder zusätzliche Mess- und Steuertechnik. Kunden haben auch die Möglichkeit, ihre eigenen Apparaturen vorübergehend in die Pilotanlage zu integrieren, um den Prozess möglichst realitätsnah abzubilden.
Inhalte / Die verfügbare Ausstattung umfasst:
1. Laboranlage mit Dünnschichtverdampfer
3. Dünnschichttrockner (vertikal und horizontal)
5. VISCOFILM-Dünnschichtverdampfer
Abbildung 1: Das Diagramm zeigt die Anwendungsbereiche der verschiedenen Verdampfungstechnologien. Durch die Wahl bzw. Kombination der richtigen Technologien ist GIG Karasek in der Lage, ein sehr breites Spektrum an unterschiedlichen Substanzen zu verarbeiten und diese auch weitgehend im Technikum abzubilden. @ GIG Karasek
1. Laboranlage: Erforschung der Machbarkeit und Identifizierung prozessrelevanter Faktoren
Im Fokus der Laboranlage steht die Bewertung der Machbarkeit. Es gilt zu klären, ob das Produkt erfolgreich separiert werden kann und ob der Prozess technisch umsetzbar ist.
Dabei spielt die effektive Verdampfung des Materials eine entscheidende Rolle, wobei auch atmosphärische Druckverhältnisse und potenzielle Vakuumbedingungen berücksichtigt werden müssen.
Des Weiteren ist es von hoher Relevanz, potenzielle Herausforderungen bei der Verdampfung sowie weitere prozessspezifische Faktoren zu identifizieren.
Die Laboranlage besteht aus einer in Edelstahl ausgeführten Tischanlage mit einem Dünnschichtverdampfer.
Abbildung 2: GIG Karasek Laboranlage mit Dünnschichtverdampfer @ GIG Karasek
Betriebsdaten der Laboranlage im Technikum:
-
Vakuum: > 0,005 mbar abs.
-
Heiztemperatur: 20°C bis 250 °C
- Einsatzfördermenge: 0,25 bis 2 kg/h
2. Dünnschichtverdampfer: Trennung und Konzentration von anspruchsvollen Flüssigkeitsgemischen
Der Dünnschichtverdampfer zeichnet sich durch einen schonenden Verdampfungsprozess aus und findet Anwendung sowohl beim Aufkonzentrieren als auch beim Aufreinigen von Wertstoffen.
Der Verdampfer eignet sich für verschiedene Einsatzbereiche, darunter die Konzentration von strukturviskosen Medien, die Aufkonzentrierung temperaturempfindlicher Produkte und die Destillation von niedrig siedenden wertvollen Komponenten. Darüber hinaus wird er als Reboiler in Rektifikationsanlagen eingesetzt und ermöglicht die Reinigung von hochsiedenden Produkten durch Abdestillation.
Pilotanlage: Anpassung des optimalen Rotortyps
Die Dünnschichtverdampferanlage im Technikum entspricht etwa einer Trennstufe, als Heizmedium kommt Wärmeträgeröl zum Einsatz. Der Verdampfer kann mit unterschiedlichen Rotor- und Wischerblättern betrieben werden, um das volle Spektrum an Funktionen abzubilden, welches auch in der Großanlage zur Verfügung steht. Auf diese Weise können gezielt Versuche durchgeführt werden, um die bestmögliche Kombination für spezifische Kundenanforderungen oder Produkte zu ermitteln. Zusätzlich ist die Verschaltung mit einer Destillationskolonne möglich.
Die Leistung der Anlage wird über eine Massenbilanz bestimmt.
Abbildung 3: Dünnschichtverdampferanlage im Technikum © GIG Karasek
Funktionsprinzip: Kurze Verweilzeiten und minimale Temperaturbelastung
Der Dünnschichtverdampfer besteht aus einem zylindrischen, von außen beheizten Mantel, in dessen Innerem sich ein Rotor befindet. Die Rotorblätter sind so konstruiert, dass sie den Heizmantel nicht berühren. Spezielle Wischerelemente sorgen jedoch für eine gleichmäßige Verteilung des Produkts sowie den kontinuierlichen Weitertransport des Produktstroms. Gleichzeitig verhindern die Wischer eine Verkrustung oder Verblockung der Heizfläche.
Durch kurze Verweilzeiten des Produkts auf der Heizfläche und die Minimierung der Temperaturbelastung wird ein schonender Verdampfungsprozess erreicht, der eine hohe Produktqualität gewährleistet:
- Das Stoffgemisch wird zunächst aus dem Vorlagebehälter entnommen und durch einen Vorwärmer zum Apparatekopf des Dünnschichtverdampfers befördert.
- Dort wird es über ein rotierendes Verteilersystem an der Innenwand des Verdampfers aufgebracht und fließt als dünner Flüssigkeitsfilm nach unten zum Sumpf des Verdampfers.
- Während dieses Prozesses verdampfen die leicht siedenden Anteile des Gemisches (Brüden).
- Um die Verdampfungsleistung zu erhöhen, wird der Flüssigkeitsfilm mittels eines Wischersystems turbulent durchgemischt und gleichmäßig an der Heizwand verteilt.
- Der kontinuierliche Austausch des Produktstroms, der mit der Heizfläche in Kontakt kommt, ermöglicht einen schonenden Verdampfungsprozess und sorgt durch die minimierte Temperaturbelastung für die Sicherstellung einer hohen Produktqualität.
- Das resultierende Sumpfprodukt wird mittels einer Zahnradpumpe aus dem Verdampfer ausgetragen und als Konzentrat gesammelt.
- Die Brüden strömen hingegen zum Kondensator, wo sie rohrseitig niedergeschlagen werden. Das so gewonnene Brüdenkondensat wird entweder in Wiegebehältern gesammelt oder direkt in einen Sammelbehälter gepumpt.
Optimierte Stofftrennung: Verschaltung mit Destillationskolonne
Der Dünnschichtverdampfer ist im Technikum mit einer Destillationskolonne verschaltbar, um die Effizienz des Trennprozesses zu maximieren und die Herstellung hochreiner Produkte zu ermöglichen:
- Der Prozess beginnt im Dünnschichtverdampfer, wo das Stoffgemisch als dünner Film auf der beheizten Oberfläche verdampft.
- Der entstehende Brüdendampf tritt rechtsseitig aus dem Dünnschichtverdampfer aus und wird in die nachgeschaltete Destillationskolonne geleitet. Der Dampf, der normalerweise direkt zum Kondensator strömen würde, wird in diesem Fall in die Kolonne umgeleitet.
- Innerhalb der Kolonne, die aus zwei beheizten Rohrstücken besteht, steigt der Brüdendampf nach oben. Zur Verbesserung der Trennleistung sind die Rohre mit speziellen Einbauten (Packungen, Schüttgut) versehen, die nach den Vorgaben des Kunden eingebaut werden.
- Nach dem Aufstieg wird der Brüdendampf am oberen Ende der Kolonne als Kopfprodukt seitlich abgeleitet, wo Temperatur- und Druckmessungen zur Prozessüberwachung durchgeführt werden. Die schwerer flüchtigen Bestandteile des Gemisches verbleiben als Sumpfprodukt.
- Um den Brüdendampf zu verflüssigen, wird er über ein Abfallrohr nach unten in den Kondensator geleitet. Dort kondensiert er und wird schließlich als Destillat in einem Auffangbehälter gesammelt.
Ein typisches Anwendungsbeispiel für dieses Verfahren ist die Entschwefelung von Biodiesel: Im ersten Prozessschritt erfolgt die Entwässerung des temperaturempfindlichen Biodiesel im Dünnschichtverdampfer. Anschließend wird im zweiten Prozessschritt die Kolonne zugeschaltet, um den Schwefel abzutrennen.
Betriebsdaten der Pilotanlage im Technikum:
Dünnschichtverdampfer:
- Durchsatz: 10 bis 50 kg/h
- Prozessdruck: 5 mbara bis Atmosphäre
- Max. Temperatur: 340°C
Destillationskolonne:
- Höhe: 1587 mm
- Durchmesser: 107,1 mm
- 15 Trennstufen möglich
- Information: Limit der Kolonne ist der Durchsatz
3. Dünnschichttrockner: Schonende Trocknung hitzeempfindlicher Produkte
Der Dünnschichttrockner, eine Sonderbauart des Dünnschichtverdampfers, bietet eine schonende und effiziente Alternative, wenn konventionelle Trocknungstechnologien bei anspruchsvollen Anwendungen an ihre Grenzen stoßen. Der Dünnschichttrockner findet in Branchen wie Abfallentsorgung, Chemie, Pharmazie und Lebensmittelverarbeitung breite Anwendung, um eine Vielzahl von Produkten wie Schlämme, Chemikalien, Suspensionen, Pasten und feuchte Feststoffe effektiv zu trocknen.
Abbildung 4: Funktionsprinzip eines Dünnschichttrockners @ GIG Karasek
Pilotanlage: Maximale Trocknungsleistung durch Trockner-Kombination
Im Technikum stehen sowohl ein vertikaler als auch ein horizontaler Dünnschichttrockner zur Verfügung, um umfangreiche Tests und Versuche durchzuführen.
Für die Trocknung sehr nasser Schlämme empfiehlt sich eine Kombination aus Vortrocknung im vertikalen Apparat und anschließender Nachtrocknung im horizontalen Dünnschichttrockner.
Durch diese Vorgehensweise kann eine minimale Restfeuchte erreicht werden.
Abbildung 5: Horizontaltrockner in der Fertigung © GIG Karasek
Funktionsprinzip: Hohe Effizienz bei kurzer Trocknungszeit
Der Dünnschichttrockner arbeitet nach dem Prinzip des Dünnschichtverdampfers und zeichnet sich durch seine hohe Trocknungseffizienz und die Möglichkeit kurzer Trocknungszeiten aus. Mit seiner speziellen Wischerkonstruktion ermöglicht der Verdampfer eine schonende Trocknung von flüssigen Einsatzprodukten, bis hin zur Pulverform, wobei Verluste an Wertstoffen minimal gehalten werden und eine hohe Reinheit der Trockenprodukte gewährleistet ist. Ein anschauliches Praxisbeispiel finden Sie in unsern Blogbeitrag "Maßarbeit bei Power Oil Rostock, Deutschland“
Abbildung 6: Horizontaltrockner @ GIG Karasek
Betriebsdaten der Pilotanlage im Technikum:
Horizontaltrockner/Vertikaltrockner:
- Durchsatz: 10 bis 40 kg/h
- Prozessdruck: 40 mbara bis Atmosphäre
- Max. Temperatur: 230°C
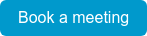
4. Kurzwegverdampfer: Hochleistungsdestillation für sensible Produkte bei niedrigem Druck
Der Kurzwegverdampfer ist eine hochentwickelte Destillationstechnologie, die speziell für die schonende Trennung empfindlicher Substanzen bei niedrigem Druck und hohen Abdampfraten konzipiert wurde. Die Kurzweg-Technologie findet hauptsächlich Anwendung in der Destillation viskoser und stark verschmutzter Produkte. Der Kurzwegverdampfer ist in der Lage, viele Substanzen zu reinigen, die mit herkömmlichen thermischen Verfahren nicht erfolgreich getrennt werden können.
Pilotanlage: Verschaltung mit Dünnschichtanlage
Der Kurzwegverdampfer im Technikum ist ein äußerst leistungsfähiger Apparat, der eine schonende Trennung empfindlicher Medien unter niedrigen Prozessdrücken im Bereich von 0,001 bis 1 mbara ermöglicht. Durch seine flexible Bauweise kann er individuell an die spezifischen Anforderungen jedes Produkts angepasst werden.
Im Technikum werden verschiedene Wischertypen getestet und variiert, um die optimale Kombination für eine effiziente Trennung zu finden.
Ein zusätzlicher Vorteil der Pilotanlage besteht darin, dass der Kurzwegverdampfer mit den Dünnschichtverdampfer-Apparaten verschaltet werden kann, um verweilzeitkritische Eindampfprozesse zu simulieren und eine realitätsnahe Untersuchung und Optimierung dieser Prozesse zu ermöglichen.
Abbildung 7: Dünnschichtanlage im Technikum © GIG Karasek
Funktionsprinzip: Maximale Effizienz durch integrierten Kondensator
Im Wesentlichen funktioniert ein Kurzwegverdampfer nach dem gleichen Hochleistungsprinzip wie der Dünnschichtverdampfer, jedoch mit zwei entscheidenden Unterschieden:
- Feinvakuum: Das Produkt wird im Feinvakuum (0,001 bis 1 mbara) destilliert, um die Siedetemperatur zu senken und somit eine unerwünschte Reaktion oder Zersetzung thermisch-sensibler Produkte zu vermeiden.
- Integrierter Kondensator: Im Gegensatz zu herkömmlichen Verdampfern ist der Kondensator direkt im Verdampfer integriert. Dadurch wird der Weg der Brüden, also der verdampften Bestandteile, zum Kondensator extrem verkürzt, wodurch der Druckverlust minimiert und eine hohe Abdampfrate ermöglicht wird.
Durch diese spezielle Bauweise und das Feinvakuumverfahren eignet sich der Kurzwegverdampfer besonders für die schonende Destillation empfindlicher Substanzen wie Fettsäuren, halbflüchtige Aromastoffe, Vitamine und Öle.
Abbildung 8: Kurzwegverdampfer Funktionsprinzip @ GIG Karasek
Betriebsdaten der Kurzwegverdampfer-Pilotanlage im Technikum:
- Durchsatz: 10 bis 100 kg/h
- Prozessdruck: 0,005 mbara bis 1 mbara
- Max. Temperatur: 340°C
5. VISCOFILM – Dünnschichtverdampfer: Schonende Verarbeitung von hochviskosen Fluiden
Der VISCOFILM-Dünnschichtverdampfer wurde speziell für die schonende Verdampfung von Produkten mit einer hohen Viskosität von bis zu 5.000 Pa·s entwickelt. Er fungiert als Verbindungsglied zwischen herkömmlichen Dünnschichtverdampfern, die für Flüssigkeiten mit einer Viskosität unter 10 Pa·s ausgelegt sind, und Polymerextrusionstechnologien, die Flüssigkeiten mit einer Viskosität von bis zu 10.000 Pa·s verarbeiten können.
Funktionsprinzip: Hochleistungsverdampfer für nachhaltige Anwendungen
Der VISCOFILM-Dünnschichtverdampfer basiert auf dem Funktionsprinzip eines Dünnschichtverdampfers, weist jedoch einige besondere Merkmale auf. Vor allem sein individueller und modularer Aufbau sowie das spezielle Rotor-Design zeichnen ihn aus und ermöglichen eine vielseitige Anwendung und einen breiten Einsatzbereich.
Ein besonderer Schwerpunkt des Hochviskosverdampfers liegt auf der Verwertung von nachwachsenden und/oder recycelbaren Stoffen, wie zum Beispiel Polymeren. Durch seine spezielle Konstruktion ermöglicht er nicht nur die effiziente Rückgewinnung von Lösemitteln, sondern auch die Minimierung der Restgehalte in den Endprodukten. Der Hochviskosverdampfer eröffnet somit nicht nur ökonomische Vorteile, sondern trägt auch zur Reduzierung der Umweltbelastung und zur Schonung wertvoller Ressourcen bei.
Abbildung 9: VISCOFILM-Dünnschichtverdampferanlage im Technikum © GIG Karasek
Pilotanlage: Robuste Anlagenausstattung für den kontinuierlichen Betrieb
Die VISCOFILM-Dünnschichtanlage im Technikum ist robust ausgeführt und sowohl für den kontinuierlichen Betrieb als auch für die Produktion von Kleinmengen geeignet:
- Für die effiziente Verarbeitung von Materialien mit hohen Viskositäten ist der Einsatz einer speziellen Einförderpumpe erforderlich, um das Material in den Verdampfer zu fördern.
- Die Beheizung des gesamten Systems ist notwendig, um sicherzustellen, dass Materialien, die bei bestimmten Temperaturen verfestigen, effektiv durch die Anlage befördert werden können. Die gesamte VISCOFILM-Anlage wird daher mit einem Doppelmantel beheizt – vom Vorlagebehälter über die Rohrleitungen und Instrumentierung bis hin zum Apparat und der Rückstandsleitung.
- Der Verdampfer und die Produktpumpen sind jeweils mit eigenen Antrieben ausgestattet, um eine präzise Steuerung und Regelung zu gewährleisten.
- Der Verdampfer erfüllt die strengen Anforderungen für den Einsatz in explosionsgefährdeten Bereichen der Zone 1.
- Der Selbstreinigungseffekt ermöglicht eine durchgängige Produktion.
Abbildung 10: Prinzipienschema Pilotanlage VISCOFILM-Dünnschichtverdampfer © GIG Karasek
Anlagenausstattung:
- Rührbehälter mit Doppelmantel
- VISCOFILM-Dünnschichtverdampfer
- Kondensator
- Kühlfalle
- Zahnradpumpen: 10 - 150 l/h, Motor mit FU
- Vakuumstation (Drehschieberpumpe / Wälzkolbenpumpe)
- Heizgerät, Kühlgerät
- Verdampfer, Produktpumpen und Vakuumpumpen
- ATEX Kategorie II 2G / 3G
- Temperiergeräte und Schaltschrank in Ex-freier Zone
Optimierte Integration von Extruder und VISCOFILM-Verdampfer
Ein besonderes Merkmal des VISCOFILM-Verdampfers ist der standardmäßig vorhandene Anschluss für einen Extruder. Es besteht somit im Technikum die Option, Granulat direkt in einem temporär zur Verfügung gestellten Extruder aufzuschmelzen und anschließend in den VISCOFILM-Verdampfer zu leiten.
Ebenso ist die nachgeschaltete Integration des Extruders möglich. Ein anschauliches Beispiel hierfür ist die kundenseitige Installation eines Kühlers im Technikum, um den Prozess nach der Verarbeitung im VISCOFILM-Verdampfer mit einem Extruder fortzusetzen. Der Kühler wurde gezielt eingesetzt, um das Produkt von einer Verdampfungstemperatur von 240°C auf 200°C abzukühlen, bevor es granuliert wurde. Zusätzliches Equipment wurde vom Kunden bereitgestellt, um über einen Zeitraum von einer Woche realitätsnahe Versuche durchzuführen und den Prozess optimal zu simulieren.
Betriebsdaten der VISCOFILM-Pilotanlage im Technikum:
- Durchsatz: 10 bis 150 kg/h
- Prozessdruck: 0,001 mbara bis Atmosphäre
- Max. Temperatur: 340 °C
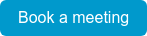
6. Röhrenfallfilmverdampfer: Standardanwendungen für Medien mit geringer Verschmutzung und Viskosität
Röhrenfallfilmverdampfer kommen in zahlreichen Standardverfahren zum Einsatz, bei denen Flüssigkeiten konzentriert, Stoffgemische getrennt oder Wertstoffe zurückgewonnen werden müssen. Durch ihren kompakten Aufbau sind sie besonders gut geeignet für Anwendungen mit geringen Eindampfleistungen. Bedingt durch ihre anspruchsvollen Reinigungsanforderungen werden sie jedoch bevorzugt in Industriezweigen eingesetzt, in denen Medien mit niedriger Viskosität und geringem Verschmutzungsgrad verwendet werden.
Pilotanlage: Mehrstufige Prozesse und Versuche mit aggressiven Medien
Im Technikum werden üblicherweise Versuche durchgeführt, um die Eignung des Röhrenfallfilmverdampfers für spezifische Anwendungsbereiche zu bewerten und optimale Betriebsparameter zu ermitteln. Darüber hinaus dienen die Versuche der Entwicklung und Validierung von Prozessmodellen für die Skalierung und den Einsatz von Röhrenfallfilmverdampfern in verschiedenen Industriezweigen.
Ein wichtiger Faktor dabei ist die Berücksichtigung der Verschmutzung, die zu einer Verringerung der Wärmeübertragungseffizienz und zu einer verminderten Verdampfungsleistung führen kann. Es bietet sich zudem die Möglichkeit, durch die Verbindung des Fallfilmverdampfers mit dem Dünnschichtverdampfer mehrstufige Prozesse zu simulieren.
Funktionsprinzip: Effiziente Verdampfung durch Wärmeaustausch und Schwerkraft
Röhrenfallfilmverdampfer sind vertikal angeordnete Rohrbündelwärmetauscher, die durch die Kombination von Wärmeaustausch und Schwerkraft eine effiziente Verdampfung mit hohen Abdampfraten ermöglichen:
- Das Produkt wird über die Verteiltasse in der oberen Apparatehaube in den Verdampfer eingespeist und fließt in einem dünnen Film an den Innenwänden der von außen beheizten Rohre hinunter.
- Die leichter flüchtige Fraktion verdampft an der Heizfläche und wird unter Einfluss der Schwerkraft im Gleichstrom mit den Konzentrat nach unten gefördert.
- Anschließend erfolgt in der unteren Verdampferkammer die Trennung der dampfförmigen Phase (Brüden) von der flüssigen Phase (Konzentrat).
- Mitgerissene Tropfen werden über integrierte Tropfenabscheider oder Zyklonabscheider vom Brüdendampf abgetrennt.
- Der Brüdendampf wird kontinuierlich abgeführt, während das Konzentrat am unteren Ende des Verdampferkörpers mithilfe einer Umwälzpumpe in die nächste Verdampferstufe oder den nächsten Prozessschritt geleitet wird.
Abbildung 11: Der Röhrenfallfilmverdampfer basiert auf dem Prinzip eines Rohrbündelwärmetauschers @ GIG Karasek
Betriebsdaten Röhrenfallfilmverdampfer:
- Röhrenfallfilmverdampfer in zwei Größen
- Produktkondensator mit Produktkühler
- Verdampfungsleistung: ca. 500 bis 2.000 kg pro Versuchstag
7. Destillationskolonne
Destillations- bzw. Rektifikationskolonnen finden in vielen Bereichen der chemischen Industrie Anwendung, insbesondere bei der thermischen Trennung komplexer Vielstoffgemische. Sie sind besonders vorteilhaft, wenn Fraktionen weiter aufgetrennt und höhere Reinheiten erzielt werden müssen. Häufige Einsatzfelder sind die Aufreinigung von wiederverwertbaren Substanzen, die Raffination von Erdöl sowie die großtechnische Herstellung von Grundchemikalien.
Pilotanlage: Aufreinigung und Trennung von Vielstoffgemischen
Neben der mit dem Dünnschichtverdampfer kombinierbaren Kolonne verfügt das Technikum auch über eine eigenständig betriebene Destillationskolonne. Typische Versuchsanwendungen umfassen die Aufreinigung von Stoffgemischen und die Trennung von Feedströmen mit Komponenten ähnlicher Siedepunkte, wie beispielsweise die Aufbereitung von Lösemitteln wie Ethanol oder die Trennung von Fettsäuren und Harzsäuren aus Tallöl.
Zur Optimierung des Stoffaustauschs wird die Kolonne mit Packungen oder Schüttgut ausgestattet, wodurch die Oberfläche vergrößert und der Kontakt zwischen Dampf und Flüssigkeit maximiert wird. Vom Kunden gewünschte Einbauten können für Versuchszwecke beigestellt und von GIG Karasek in die Kolonne eingebaut werden.
Anmerkung: Wenn keine erhöhten Trennschnitte einer Kolonne benötigt werden, beispielsweise bei der einfachen Trennung von Schwer- und Leichtsiedern wie bei der Biodieselproduktion, ist der Kurzwegverdampfer oft eine kostengünstigere und weniger aufwendige Alternative. Mehr dazu in unserem Blogbeitrag „Biodiesel-Destillation: Warum der Kurzwegverdampfer im Vergleich zur Rektifikationskolonne die bessere Option ist“.
Funktionsprinzip: Hohe Reinheitsgrade durch Gegenstromprinzip
Das Prinzip der Rektifikationskolonne beruht auf der thermischen Trennung von Flüssigkeitsgemischen durch wiederholtes Verdampfen und Kondensieren. Aufsteigender Dampf und herabfließendes Kondensat interagieren kontinuierlich im Gegenstrom, wodurch die Trennleistung erheblich verbessert und hohe Reinheiten der Einzelkomponenten erreicht werden.
- Das Flüssigkeitsgemisch wird im Sumpf der Kolonne erhitzt, sodass die flüchtigeren Komponenten verdampfen, in der Kolonne aufsteigen und sich anschließend im nachgeschalteten Kondensator verflüssigen. Der schwerer siedende Anteil wird kontinuierlich aus dem Sumpf abgezogen und entsorgt.
- Das Destillat wird zum Großteil als Kopfprodukt abgezogen, während ein kleiner Anteil als Rückfluss in den Kolonnenkopf eingespeist wird, um die Einbauten zu spülen und eine kontinuierlich saubere Abtrennung sicherzustellen.
- Der während des Aufsteigens in der Kolonne kondensierende Dampf fließt als flüssige Gegenphase wieder abwärts. Durch den Stoff- und Wärmeaustausch des nach oben steigenden Dampfes und der nach unten fließenden Gegenphase erfolgt die Trennung des Flüssigkeitsgemisches.
- Die wiederholte Durchführung des Destillationsvorgangs steigert den Gehalt an leichter flüchtigen Komponenten in jedem neuen Destillat bis hin zur vollständigen Trennung des Flüssigkeitsgemisches.
Betriebsdaten Destillationskolonne:
- Höhe: 3342 mm
- Durchmesser: 108 mm
- Div. Füllkörper und Packungen möglich (je nach Kundenwusch)
8. Fazit: Erforschen, entwickeln, optimieren
Das Technikum von GIG Karasek stellt eine hochmoderne Testinfrastruktur und ein Team erfahrener Spezialisten bereit, um Trennverfahren zu erforschen, zu entwickeln und zu optimieren. Mit flexiblen Anlagen, die vielseitige Temperatur- und Druckbereiche abdecken, sowie der Möglichkeit zur Integration kundeneigener Apparaturen bietet es eine umfassende Plattform für Labor- und Pilotversuche. Kunden können hier die Trennleistung, Reinheit und Qualität ihrer Produkte verbessern und maßgeschneiderte Lösungen für ihre individuellen Anforderungen finden.
Als Kompetenzzentrum für innovative Trenntechnologien unterstützt das Technikum bei der Realisierung maßgeschneiderter Lösungen und ist der ideale Partner für die Entwicklung optimaler Prozesslösungen. Kontaktieren Sie uns gerne, um Ihre spezifischen Anforderungen zu besprechen.
Besuchen Sie unseren Newsroom!
Hier finden Sie aktuelle NEWS, unseren EVENTKALENDER oder weitere INSIGHTS zu Schwerpunktthemen.
Zum Thema Technikum haben wir bisher folgende Artikel veröffentlicht:
GIG Karasek Technikum: Wie Sie unter realen Bedingungen neue Konzepte erproben
Von Abwasser bis Polymerschmelzen: Effiziente Produktversuche im GIG Karasek Technikum
MINIPLANTS - Die Brücke zwischen Labor und Produktion